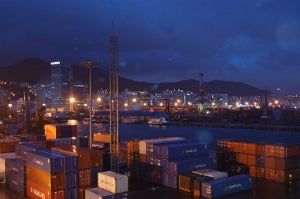
For manufacturing and construction companies, plasterboard waste is a costly nuisance.
Thousands of dollars can be saved each year through the reduction of plasterboard waste. One way to achieve this is to ensure that plasterboard stays intact during container loading, transit and unloading. A few correct decisions in this process will make a big difference. I discuss three ways to reduce plasterboard waste.
1. Use a container loader with smart technology.
As plasterboard is so fragile, a single bump against a container wall can damage it. Choose a container loader with the latest technology. Features to look for include position feedback sensing systems that calculate the load’s distance from the container wall to avoid any bumping, hydraulic lifting, and manual steering. Being able to load materials from different sides of the container is also an advantageous feature.
Around 17% of drywall is said to be wasted during the manufacturing and installation processes. This is a huge burden on a company’s budget, but the good news is that it can be drastically reduced. In fact, one company in Queensland, Australia, was able to reduce its plasterboard damage levels from 16% to less than 1% within one year by practicing these steps.
2. Choose the right transport method.
Plasterboard may be transported by rail, road or sea.
- Rail – Transporting by rail gives carriers the advantage of avoiding traffic, and also makes civilians happy by minimising the number of trucks on the road. However, it comes with the occupational hazard of shunting, which is also an opportunity for damage to fragile materials such as plasterboard. There’s also the existence of railroads that cannot accommodate double-stacked containers, or sections of rail networks with insufficient vertical clearance for high-cube containers.
- Road – Most local suppliers and distributors use trucks to transport plasterboard. This tends to be the more affordable solution for such users, but the obvious risks posed to plasterboard include being handled more frequently, and exposure to the elements and surrounding cargo.
- Sea – Shipping by sea tends to be a cheaper option for large-scale suppliers of plasterboard. It is a practical choice for long-distance or cross-country deliveries, as well as for bulk orders. Transporting plasterboard by sea also means not subjecting the materials to the potentially damaging process of shunting.
3. Secure the load well.
Methods to secure loads in containers have not radically changed over the years, with steel strapping, polyester strapping, wood blocking, and bracing, and the use of ratchet tie-down straps being some of the most common or preferred techniques.
But one aspect of securing loads has seen innovation and improvement, that of container loading systems and stackers. For instance, the Tynecat container loader will be upgraded to allow 190mm or less dunnage loss. Technologies like this, along with equipment like rotator stackers, help in improving container capacity utilisation. Higher packing density not only helps you save money, but also allows the materials less room for shifting during transport.
It is easily damaged at any stage of the construction process, from manufacture and shipping to storage, distribution and mounting.
All this results in enormous waste each year, more than 15 million tons of gypsum waste is landfilled annually in Europe, the US, and Asia, according to Gypsum Recycling International. A study by Envirowise estimates that one in every eight sheets of plasterboard bought and delivered to a construction site in the UK is wasted, while another research paper states that more than 20,000t of plasterboard waste is disposed of in the Auckland region alone every year. Apart from being an unwanted environmental load as landfills reach capacity, all this translates into a needless expense for manufacturing and construction companies, and a thorn in the side of every operations or logistics manager.
In response, governments are regulating the amount of gypsum waste allowable in landfills, and recycling companies are reprocessing plasterboard waste into gypsum powder, which is reused as raw material for creating plasterboard.