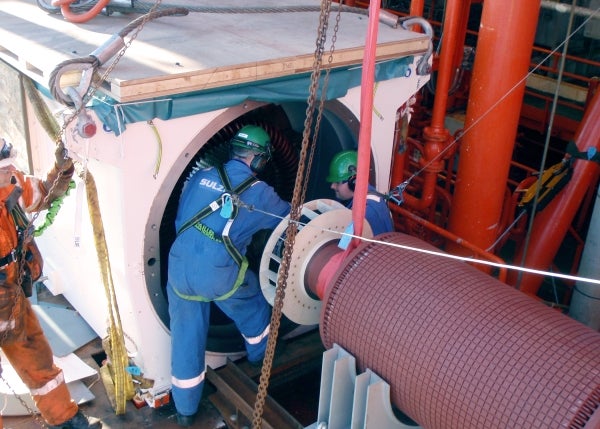
As the trend for passenger ferries and cruise ships to increase in size continues, the requirement for reliable and effective back-up systems remains a constant.
Modern vessels can deal with the failure of a generator without affecting passenger comfort, but completing the repair while remaining at sea requires a dedicated and skilled team of engineers. Graeme Robertson, Head of Operations UK for Sulzer’s Birmingham Service Centre, looks at the essential requirements for efficient on-board repairs.
One of the most critical systems on-board ships is the power generation system, which is obviously required for electrical power but is also increasingly used to supply propulsion systems. Due to the essential nature of the generators, modern design specifications ensure that the vessel can continue to operate normally, even if an issue has caused a main generator to be taken offline.
One of the key aspects to managing a generator failure effectively is assessing the root cause of the failure and completing the repair as quickly as possible in order to restore the full generating capacity with its built-in redundancy.
However, the cost of doing this, in terms of lost revenue while the vessel is docked would be substantial, so the preferred method is to complete repairs while still at sea.
Root cause analysis is essential if the repair to the generator is going to be effective, because without it there is a substantial risk of completing a repair without fixing the cause, which will lead to similar failures in the future. In some cases the OEM design may need to be modified to provide more reliable operation, while in others the use of high-quality insulating materials and coil manufacturing techniques will provide the solution.
In order to keep the repair process as brief and as simple as possible, it is usually better to select a repairer that can complete the entire project and so avoid any confusion in the responsibilities of different contractors, which can cause delays.
Experience in this field counts for a great deal as no two generator installations are the same and the ability to apply expert knowledge to a difficult situation can save valuable time.
Speed is of the essence in these situations and for the project to be completed as efficiently as possible requires all the necessary resources available at the same time and the ability to deploy them at a moment’s notice. When a generator requires a complete stator rewind in-situ, the scale of the operation to support the engineers on-board is substantial.
At Sulzer, a coordinated approach means that a complete team, comprising field engineers, design engineers, rewind facilities and project management experts, is dedicated to a project as soon as a repair request is approved. The Southampton and Falkirk Service Centres are at the heart of the marine repair business and have provided complete generator repair services for many years.
One recent example was the repair of a 7.5MW generator on a cruise-liner that had suffered from a stator winding fault that would require a complete strip-down and new windings to be manufactured and installed. Once the repair team was on-board they worked with the ship’s engineers to dismantle the generator and determine the exact fault with the original windings.
Inspection of the stator revealed that the OEM design of the coils had a flaw, which had caused the generator to fail.
Sulzer suggested a modification to the design to ensure that a similar failure would not reoccur and this was incorporated with the rest of the coil design details and sent to Sulzer’s Birmingham Service Centre in the UK, where the coil shop started work on manufacturing the new coils.
While the new coils were being produced, the on-site engineers finished stripping and cleaning the stator so that as soon as the new coils arrived they could be installed and connected. With the new windings in place, they underwent a full series of tests to check the performance and the insulation resistance.
Once complete, a temporary oven was created around the stator and the windings were cured in-situ, before the epoxy resin coating was applied and the windings were finish painted with a varnish-based paint. The generator was reassembled before testing, commissioning and finally returning it to normal service.
The entire repair project was completed in just seven weeks, with the teams working round the clock, which ensured that there was no interruption to the ship’s schedule, no inconvenience to the passengers and no additional costs for docking the vessel.
Careful monitoring and maintenance procedures will help ensure reliability in on-board equipment, but when the time comes to implement a major repair project it is essential to minimise the cost and the inconvenience to passengers.
On-board repairs offered the perfect solution in this case, especially when compared with the lengthy and costly alternative of a dry dock and a large hole being cut in the hull to allow the generator to be removed for a land-based repair.