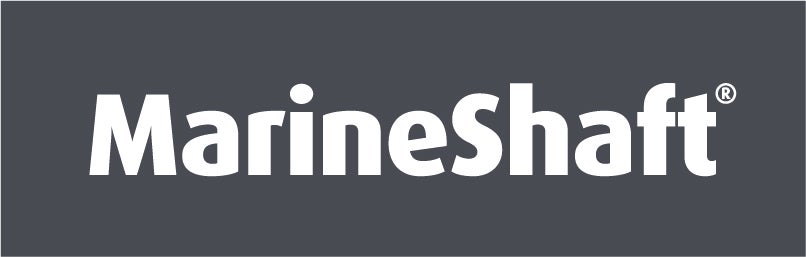
When crucial components like shaft seal liners suffer damage, owners face the need for urgent replacement or repair solutions.
Time is money, and speed of delivery plays a crucial role in the decision-making process. The cases we share with you in this newsletter are good examples:- Urgent repair of two Duplex Shaft seal liners for Tunnel Thruster
- Urgent repair of damages on a crankshaft coupling end
In a recent case, we successfully repaired two damaged Shaft liners for a tunnel Thruster in only 4 days.
We received an inquiry from our French client to repair or replace the liners. Based on the received pictures and measurements of the damage, we suggested repair by laser cladding of the two Duplex Seal Liners. The vessel M/V Wind of Change was docked in Poland and our client shipped the Shaft seal liners to our workshop in Denmark. Each liner measured Ø339,85/270 x 185,5 mm.Once in our workshop:
The liners had a surface layer of chromium, which we removed by machining, after which we conducted a liquid penetrant test of the surface. We applied Stellite by laser cladding, a process which adds 0,8 mm of material with each layer applied. The new material fuses to the base material, and an even harder and more wear resistant surface is obtained. We machined the rough laser cladded surface, back to the original dimensions and a second liquid penetrant test confirmed the quality of the laser cladded area, thus completing the final inspection. We arranged a swift transport of the liners back to the vessel and had the job completed in 4 days.In this case, 3 layers were sufficient to rebuild to original dimensions, but additional layers can be applied if needed, as you can read about in the next case.
Crankshaft repair
We completed another urgent repair this week. Our engineers worked throughout the weekend to finish the repair quickly.
Case: The crankshaft had sustained damage to the coupling end and the customer had previously made a temporary repair by shrink fitting a ring on the coupling end. Now the customer had to find a permanent solution, and they contacted us to discuss our repair proposal. We recommend a repair by laser cladding to rebuild the surface to original dimensions. Upon receiving the crankshaft in our workshop, we meticulously skimmed the surface to prepare for laser cladding and NDT. The laser cladding process of rebuilding the coupling end began. In total, we applied 16 layers of Inconel 625, each adding 0,8 mm of material. After completing the laser cladding, we machined the repaired surfaces, and a final NDT was carried out by an independent third-party company. In just three days, we repaired the crankshaft with approval from DNV.Expansion – Purchase of another and larger laser cladding system
We recently acquired another laser cladding system, which is performing exceptionally well. The repair case described earlier was carried out with this new equipment.
Capacity boost
With two laser cladding systems, we ensure capacity for urgent requests, and most of our laser cladding repairs are related to breakdowns where fast action is crucial. Another important reason for this expansion is to provide more repair possibilities. This new system has an extended reach in cavities and is easier to move around with its continuous tracks. The robot arm can lift 45 kg of equipment compared to the other systems 10 kg capacity.
We have acquired a new laser lance
With the new lance, which has a reach of approx. 700 mm, MarineShaft can repair internal damages in larger components such as couplings and cylinders. The new lance can fit into openings as small as Ø170 mm. The new lance is compatible with both of our laser cladding systems. A new job is waiting in our workshop already: a cylinder block from a 1962-build B&W Alpha engine. We need the reach of this new lance for this repair.