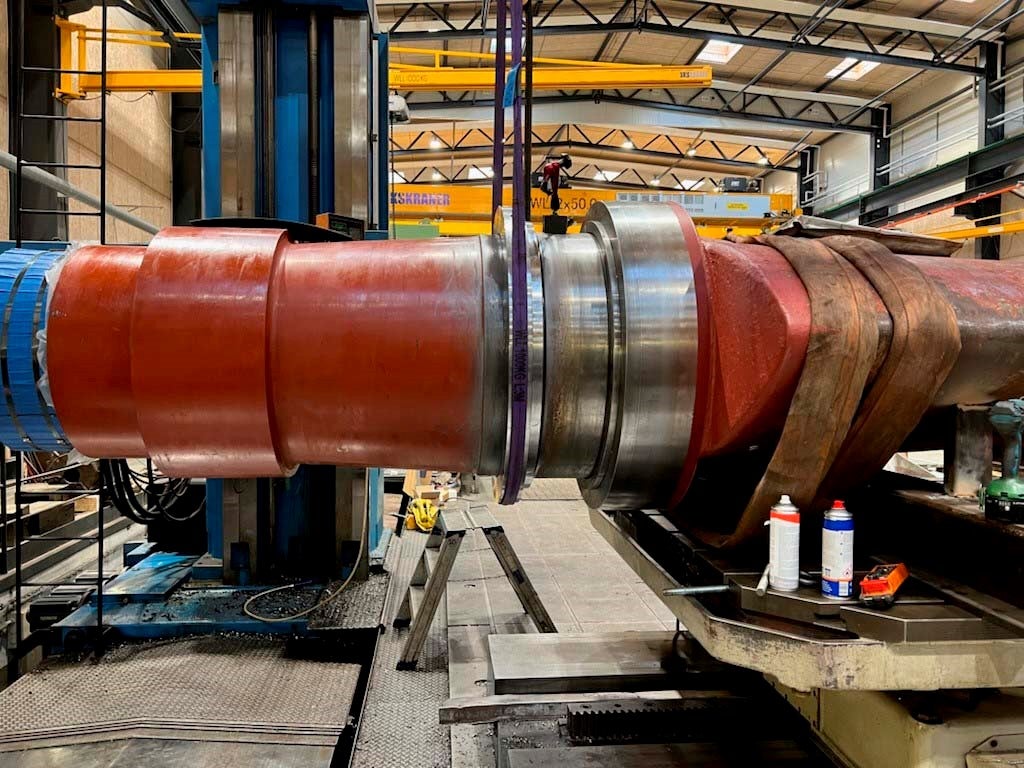
MarineShaft recently completed two repair jobs using laser cladding technology.
The ferry had experienced failures in the stabiliser system with leaks. The sealing surfaces suffered from wear, and we suggested repair by laser cladding.
During a planned docking the stabiliser fins were sent by truck to our workshops in Denmark.
Each stabiliser fin weighed 25 tons and was too big to place in our lathes for turning, so we programmed our numerically controlled laser cladding equipment to move circularly, and the fin could be placed on the floor in the workshop.
We used a stainless-steel material/powder to build up the surface. Our laser cladding equipment applies 0.8mm of material per layer, and we welded up four layers of Inconel 625 for this repair.
A specially designed tool did the machining
Using our lathes was not an option, and we had to find a different solution to machine the sealing surface before and after laser cladding.
Often, we have developed purpose-built tools, and for this repair, we adjusted one of those to fit one of our horizontal boring machines in the workshop. It worked brilliantly.
The repair was completed within the scheduled docking time, and the ferry is back at sea and ready to take passengers on a steady course.
Laser cladding of hub
Laser cladding is ideal for repairing hub seal surfaces. For this repair, we applied two layers of Bronze.
We perform a Liquid penetrant inspection before and after laser cladding, including machining. The involved classification society in this case was RINA.
Advantages
Laser cladding leaves minimum heat input, and post-weld-heat treatment is unnecessary.
The metal binds 100% to the basic material and creates an even harder and more resistant surface.