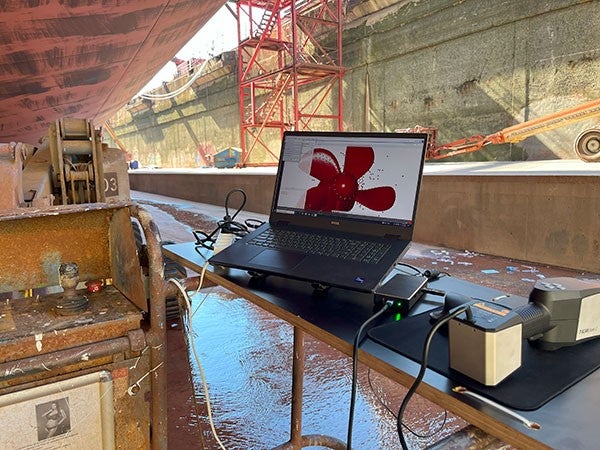
When a passenger vessel experienced noise and vibrations from its propellers, MarineShaft was contacted to perform a 3D scan while in drydock. With our handheld 3D equipment, it was possible to scan each blade, without dismantling the propellers, and make an accurate comparison to detect any deviations.
Reference markers are placed all over each propeller blade to facilitate the measurement. We have other methods to measure depending on the size, purpose, and parts you need to scan.
This 3D scanning revealed a difference in the blade’s surface geometries and, with the provided data, our customers could take action based on the scanning report.
Two of our welding technicians went to the shipyard and completed the on-site modification and repair of the propellers in two days.
3D scanning used for virtual blue-fit testing of a new tail shaft cone for the propeller
As you know, we keep a comprehensive inventory of raw materials, all of European origin and class-certified, to offer you a swift manufacturing time for new shafts, rudder stocks, and components.
To ensure precise manufacturing, we sent a technician to the vessel’s location abroad to perform a 3D scan of the fixed propeller cone and the old tail shaft. The scan data can reveal if there are any geometrical deviations inside the propeller cone. MarineShaft uses the 3D scanning data to machine the cone of the new tail shaft to the exact final dimensions.
By utilising 3D scanning data, we can conduct a virtual, blue-fit test, eliminating the need to bring the fixed propeller into the workshop. We can manufacture the new tail shaft with the correct dimensions ready for immediate installation.
The job included manufacturing new bolts and nuts, and our customer sent the intermediate shaft to our workshop so we could machine the flange and the flange holes.
The project was started on 27 August 2024 and completed on 1 October 2024.