Fierce competition, shortages of skilled workers, and full orderbooks have created a “perfect storm” for many shipyards and engineering companies. Attracting new talent to the ship design and building industry has become increasingly difficult, especially for smaller and mid-sized shipyards. In countries like Japan and Korea, the problem is amplified by demographics.
This comes at a time when shipyards are seeing increased demand for newbuilds, with some orderbooks full until 2027 and beyond. Many are already facing delivery delays as a consequence of staff shortages. Adding to the challenge are increases in material costs, with steel prices remaining high, while inflation has pushed labour costs to historical highs.
Without action to maximise the productivity of their existing workforce, both in design and construction teams, shipyards will not be able to seize the opportunities of a booming market, in which newbuild prices are nearing all-time highs. In the long run, they risk losing market share to their competitors.
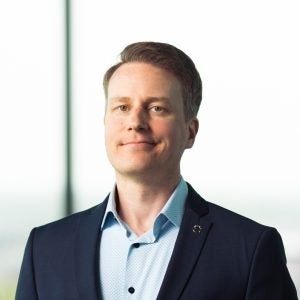
Adding to an already complex picture, shipyards are not only competing for newbuild orders; they are also seeking to position themselves and develop their skillsets in emerging markets for vessels propelled with new fuels and technologies.
The capacity to innovate will be a key differentiator going forward. Therefore, those players that can reduce delivery times and create better designs, all while maintaining financially healthy businesses, will gain a competitive edge.
How to be smart
With all those factors coming together, boosting efficiency through innovative processes is more than a “nice to have” for shipyards; those productivity improvements are critical to future-proof their businesses. This is leading to a fundamental shift: an acceleration in the digital transformation of the ship design industry.
A strong example of how digitalisation is embedding itself in shipyards’ strategy is HD Hyundai Heavy Industries, the world’s largest shipyard, which has entered a joint development project with NAPA and CADMATIC to develop a “digital shipyard”.
The vision is to harness advanced 3D models and the latest developments in information management technology to optimise the ship design and building process. This will help the company achieve shorter schedules, lower costs, and higher quality in larger and more complex projects.
In practice, the project will develop a next-generation ship design and information management system that will transform workflows, ensuring data consistency throughout the ship design process to save time and limit the risk of error. It will also enhance collaboration between the different departments and improve information-sharing between the hundreds – if not thousands – of people involved in the ship design and building process.
This will help HD Hyundai Heavy Industries respond to growing shipowner demand for innovative energy-efficient designs and enhance its capacity to deliver next-generation ships powered by alternative fuels or equipped with new technologies, including batteries or wind propulsion.
Digital and green go hand-in-hand
Streamlined processes and efficient communication are prerequisites for the era of fast-paced innovation ahead. This is because integrating new fuels and technologies brings new layers of complexity to the ship design process, requiring naval architects and engineers to explore unchartered technological territories.
A strong digital foundation makes this innovation possible in a number of ways. Using 3D models as a “single source of truth” from the very early stage and throughout the design process will enable concurrent engineering, where the different disciplines involved in a ship design can work simultaneously. This saves tremendous time and limits the risks of inconsistencies as the project progresses.
3D capabilities are also increasingly used for classification approvals, allowing surveyors to perform checks directly using the 3D model that was created to design the vessel, rather than requiring multiple lengthy conversions to 2D drawings. Early adopters of “3D model-based approvals” already report efficiency gains and improvements in the quality of designs.
Operational simulation capabilities open a game-changing opportunity for designers and engineers.
Furthermore, operational simulation capabilities open a game-changing opportunity for designers and engineers: testing the viability of completely new concepts from the early design phases. By combining 3D models with weather and operational data, they can virtually trial different iterations and predict how the future ship will perform on the specific routes where it will be operated.
In practice, this will help them determine optimal configurations for ships powered by ammonia, methanol or batteries, or assess the impact of energy-saving appliances like wind propulsion – whilst ensuring the vessel’s safety and stability.
In the longer term, the ongoing information and technology revolution will unlock a world of opportunity for shipyards, from digital manufacturing to digital twins that could create value throughout a ship’s lifecycle – helping optimise operations and maintenance schedules, for example.
The road ahead is both challenging and exciting. Companies that harness digital capabilities to improve their efficiency will not only save time and add value to their designs today, but they will also build the right foundations to remain competitive in the markets of the future. In other words, shipyards that miss the digital boat today will lose out on business tomorrow.