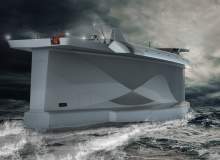
Accounting for approximately 3% of the world’s greenhouse gases – according to the European Commission – the global maritime sector is under pressure to join the environmental party and go green.
And it would appear that most industry stakeholders – including the shipyards and shipping companies – are taking appropriate steps to reduce their emissions and become more sustainable.
Of course, they don’t have much of a choice. Regulations such as MARPOL Annex VI – as mandated by the International Maritime Organisation – currently require vessels to limit their fuel sulphur content to 0.10%. By 1 January 2020, the threshold will drop to 0.5%.
That’s not to mention the IMO’s introduction of emission control areas (ECAs) in the likes of the Baltic and North Seas, as well as off the eastern seaboard of the US, aimed at curbing sulphur emissions at sea.
But going green isn’t cheap, and switching from traditional bunker fuels to low sulphur and nitrogen equivalents has already led to shipping groups feeling the pinch. Other alternatives, including the implementation of scrubbing systems, have also raised concerns over cost-efficiency.
How well do you really know your competitors?
Access the most comprehensive Company Profiles on the market, powered by GlobalData. Save hours of research. Gain competitive edge.
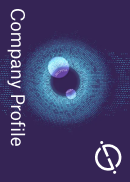
Thank you!
Your download email will arrive shortly
Not ready to buy yet? Download a free sample
We are confident about the unique quality of our Company Profiles. However, we want you to make the most beneficial decision for your business, so we offer a free sample that you can download by submitting the below form
By GlobalDataTherein lies the overriding quandary for industry players: how do they become more eco-friendly without pricing themselves out of the market?
Designer Teje Lade, who heads up Norwegian firm Lade, believes he might have the answer.
The central goal, explains Dahl, is to help ship operators curb their CO2 emissions.
The company is currently in the process of designing a new vessel – the Vindskip (translated as Windship) – which, if realised, will run on a combination of wind propulsion and LNG-powered engines.
In an exclusive interview, Lade talks us through the Vindskip’s main features, its use of cutting-edge onboard software and potential fuel and cost savings on offer to shipping companies.
Ross Davies: Could you provide a brief background to the Vindskip? How did the concept get off the ground?
Terje Lade: I’ve worked for many years now as an engineer, and for the last ten years have been designing offshore platforms for the offshore engineering sector. In addition to that, I have also been marketing and selling Norwegian ship equipment in China, Korea and Japan for the last 15 years.
So I know the business pretty well. And, in my spare time, I’ve been working on designing speed sailing boats, and looking at how to obtain the maximum speed for a given sail’s area, reducing all drag forces in the process. The speed you can achieve by doing this is amazing. You can sail two times faster than the true wind – or the ground speed. So, if the true wind is 25 knots, you can sail at 50 knots.
This fascinated me, and at a certain point this idea – which some people call ‘greed for speed’ – was transmuted into a concern for the environment and the Earth. So I started thinking about how I could use this knowledge to design a commercial ship which doesn’t run on heavy fuels. That was the beginning of the Vindskip concept.
RD: Much has been made of the large hull, which effectively acts as a sail. How does that work?
TL: The vessel’s hull is shaped like a symmetrical airfoil going in the relative wind, which will generate an aerodynamic lift giving a pull in the ship’s direction – within an angular sector of the course. It acts as the Vindskip’s wind power system.
Second to that, there is also cruise control, which makes use of an LNG-powered propulsion system. From starting the ship from zero, one can exploit the aerodynamic lift generated to create speed and save fuel.
RD: Let’s focus on the potential environmental advantages for a moment. What could it herald, particularly in light of IMO mandates, aimed at driving down the use of sulphur in engine rooms?
TL: Ship types that are particularly relevant to the Vindskip design are the so-called dry cargo ships: poll-on roll-off (RoRo) cargo ships, pure car and truck carriers and LNG-carrier membrane type, passenger and container ships.
We are currently working on an application for a RoRo, as it is quite obvious, to me at least, that this design could provide a good fit. So, over the last few months, we have been doing studies onboard sailing vessels, logging data, and also doing computational fluid dynamics studies, comparing the Vindskip design to a cargo ship.
We have found that we can carry the same cargo – perhaps a little bit more – with the Vindskip saving on about 60% of fuel. It also reduces CO2 emissions by about 80%; NOx by 90%; and SOx by 100%.
Everyone knows that the MARPOL Annex VI has been a real game-changer, but I really think the Vindskip could help shipping companies to better comply with what is being demanded of them.
Used for centuries, maritime pilots are charged with the tricky task of manoeuvring ships through dangerous and congested passages.
RD: Switching to low sulphur-content, high-quality fuel alternatives can be a costly process. Could the Vindskip model offer cost benefits to, say, a cruise company?
TL: Absolutely, yes. If you change from a heavy fuel oil to a low-sulphur fuel, the price difference is about 40-60% higher. This means extra costs for the ship owner. Of course, there are alternatives, such as scrubbing technology, which can be installed onboard a ship and effectively clean the exhaust. But this also costs money and is also very heavy – scrubbers often weigh several tonnes.
While there are still questions surrounding scrubbers, I think this may prove to be the best solution to the environmental question for the short term. But the Vindskip could provide a longer-term solution.
Due to its very low fuel consumption, Vindskip can utilise LNG as fuel and will be capable of 70 days of steaming – worst-case scenario – between bunkering. Thus it can meet all future emission requirements with lower costs.
RD: You are working in partnership with the Fraunhofer Center for Maritime Logistics and Services in Germany, which is developing the software for the Vindskip. How does it work?
TL: Using a computerised weighting of meteorological data, the programme, known as a weather routing module, can calculate a ship’s best route. By developing navigation algorithms, which give you the optimum wind angle for maximum effect of the design, you can find the best route across the ocean – whether that’s the most economical, or by ETA.
Data is also updated each day, meaning that in the event of a change of weather, the route will be updated. The software has already been tested and will be ready in March.
RD: Realistically speaking, when can we expect to see the Vindskip commercialised?
TL: Right now, we are still in the conceptual stages. The idea is being tested in wind tunnels, optimised by computational fluid dynamics and will then be tested in a model tank until a final defined form and function is reached. The tank testing is scheduled to start in April 2015.
The copyright of this form and function, protected by IPR, will then be licensed to shipping companies, consultants and shipyards.
To build the first ship, we will need a ship-owning company – its own legal entity. Then an existing management company will take care of the construction process and the running of the ship.
We estimate that the engineering and construction will take approximately two to three years. So, with a bit of luck, our first ship will be sailing by 2019.