
A team of researchers and engineers from Bristol Robotics Laboratory and Recycling Technologies is currently testing an alternative fuel made from residual mixed plastic waste, known as Plaxx, as a replacement for heavy fuel oil (HFO).
The shipping industry has relied on HFO since the 1960s. Despite being a powerful pollutant with high concentrations of nitrous and sulphur oxides, carbon dioxide (CO2) and particulates, HFO is an inexpensive and widely available option for large ship engines around the world.
Call for cleaner fuels
However, over the past few years, due to increased pressures from the global community to reduce emissions from shipping – which currently stand at 2.2% of the world’s total – as well as the surging costs of bunker fuel, shipping companies have started branching out into cleaner alternative fuels. Since 2000, bunker costs have risen by about 400%.
The International Chamber of Shipping (ICS) also describes MARPOL’s Emission Control Areas (ECAs) as “game changing” and predicts that the sulphur cap in these areas will further widen the percentage cost difference between distillate and residual fuel.
Separately from shipping, the world is faced with an increase in the global production of plastic. Currently surpassing 300 million metric tons per year, plastic production is expected to double over the next 20 years and our recycling methods cannot keep up.
According to the Ellen MacArthur Foundation, 14% of plastic packaging is collected for recycling and only 10% gets actually recycled. As such, 40% of the remaining residual plastic waste ends up in landfills, 14% is incinerated and 32% leaks back into the environment.
How well do you really know your competitors?
Access the most comprehensive Company Profiles on the market, powered by GlobalData. Save hours of research. Gain competitive edge.
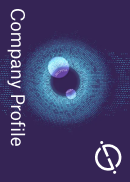
Thank you!
Your download email will arrive shortly
Not ready to buy yet? Download a free sample
We are confident about the unique quality of our Company Profiles. However, we want you to make the most beneficial decision for your business, so we offer a free sample that you can download by submitting the below form
By GlobalDataIn July, the team behind Recycling Technologies set out to address these problems. The hope is that ongoing tests will result in a new breakthrough – using Plaxx as the new cleaner, cheaper and more sustainable marine fuel.
International regulation opens up market for clean fuels
Recycling Technologies has been testing the potential of mixed residual waste plastic since 2013, after founder and CEO Adrian Griffiths opened a facility in Swindon, UK.
At the centre of their project is a machine called RT7000, which can convert residual plastic waste into a low sulphur hydrocarbon compound. The team received over £1m in funding from Innovate UK and the Engineering and Physical Sciences Research Council (ESPRC).
“We are looking for the very end of stream waste product that normally goes to a landfill or incineration,” said sales and marketing director Adrian Rupert Haworth.
They are now investigating the best uses for their invention and believe that one of the best markets for Plaxx is as a marine fuel.
Before joining the team, Haworth worked for General Electric (GE), where he completed a study on marine fuels.
“It became apparent that under the new MARPOL regulations for marine fuels, there is a need for low sulphur fuels and currently, heavy fuel oil doesn’t make the requirement.
“So the industry was looking for a low sulphur fuel and in many cases, it had to resort to distillate fuels, which is significantly more expensive.”
Indeed, vessels entering the designated ECAs under the Annex VI of the International Maritime Organization (IMO) MARPOL Convention have to use fuel with a sulphur content below 0.1%. One option is using distillate fuels, which are “at least 50% more expensive than the residual fuel that most ships would otherwise burn,” according to ICS.
Moreover, in October this year, IMO’S Marine Environment Protection Committee (MEPC) is expected to make a decision on whether to impose a global sulphur cap of 0.5%, which would come into force in either 2020 or 2025.
“There is very little sulphur in plastic, so our product, Plaxx, is ultra-low in sulphur and therefore it easily makes the requirements for MARPOL,” Haworth said.
Furthermore, global engineering consultants Ricardo, who are working in partnership with Recycling Technologies, have carried out a study on the CO2 impacts of Plaxx. Although the findings aren’t yet publicly available, “there are significant CO2 reductions if the plastic is diverted from incineration,” he said.
“We also clearly have the benefits of not having a landfill, so our goal right now is to stop pollution by converting plastic waste into Plaxx and eventually, we are looking at the potential to clean up the pollution that exists both on land and at sea.”
Testing it out in ship engines
A series of tests are currently being run on Ricardo’s Atlas II research engine, capable of evaluating the performance of fuels in large, multi-cylinder engine designs.
The next step of the trials is gauging the combustion capabilities of Plaxx compared to diesel and HFO, as well as 500-hour running trials on engines at the Recycling Technologies facility in Swindon.
“Part of the design strategy is that our equipment is modular and can be distributed. So we take the machine to the plastic,” Haworth said.
“Although we have many pieces of technology which are well-known in the industry, connecting all of them together [at] the scale we wanted has proved to be a major challenge, which we have now overcome.”
The first commercial Plaxx machine is expected to be up and running in 2017, and once proven, the team plans to replicate the technology as fast as possible.
“We foresee potentially making 100 of these [machines] a year in the not too distant future. It is intended to be very scalable, as we will mass manufacture rather than bespoke engineer on the site.”
Although the first target market will be shipping companies operating within the ECAs, the team aims to enter the international market as soon as the new global sulphur cap comes into force.
“We expect it to be quite easy to compete with other alternative fuels available [such as] LGO [light gas oil] distillate fuels. We offer environmental benefits and cost benefits,” Haworth said.
“We are working with Ricardo but also with Lloyds Marine to get the material tested to ensure we fit under the ISO 8217 marine fuel specification and, as we get the test results and start producing in quantity, we will soon be looking for trial partners.”