
As the workforce operating the world’s commercial vessels becomes less specialised and more global, automation has become tremendously important to the shipping industry. More and more shipping functions, from sophisticated navigation systems and dynamic positioning (DP) technology to propulsion control and simple alarm and monitoring systems, are ticking away without any human input.
Automation might be the best way to mitigate the potential problems of waning maritime skills, but installing these systems can be expensive. Shipping companies can gradually recoup their investment with more efficient operation and fewer onboard sailors.
Praxis Automation was established in the Netherlands in 1965, and has been developing automation systems for the shipping industry ever since. The company started with simple alarm and monitoring systems, but gradually developed increasingly advanced technology. Today, Praxis offers DP and navigation systems, as well as simulated training consoles and a host of other products under its Mega-Guard range.
Ship Technology talked to Praxis spokesman René van Lubeek about the advances that are making sailors’ jobs simpler and more productive, as well as the innovations that could drive this burgeoning market into the future.
Chris Lo: What do modern clients expect from the best ship automation systems?
René van Lubeek: First of all, they expect it to be a reliable system. That’s nothing new, of course – you’re sailing your ship far from home. But it has to be a reliable and ruggedised system, well-suited to the environment of a ship at sea. It also has to be a user-friendly system, because there are many nationalities aboard ships. With a crew change, people come onboard and have to work with the system immediately, so it has to be intuitive.
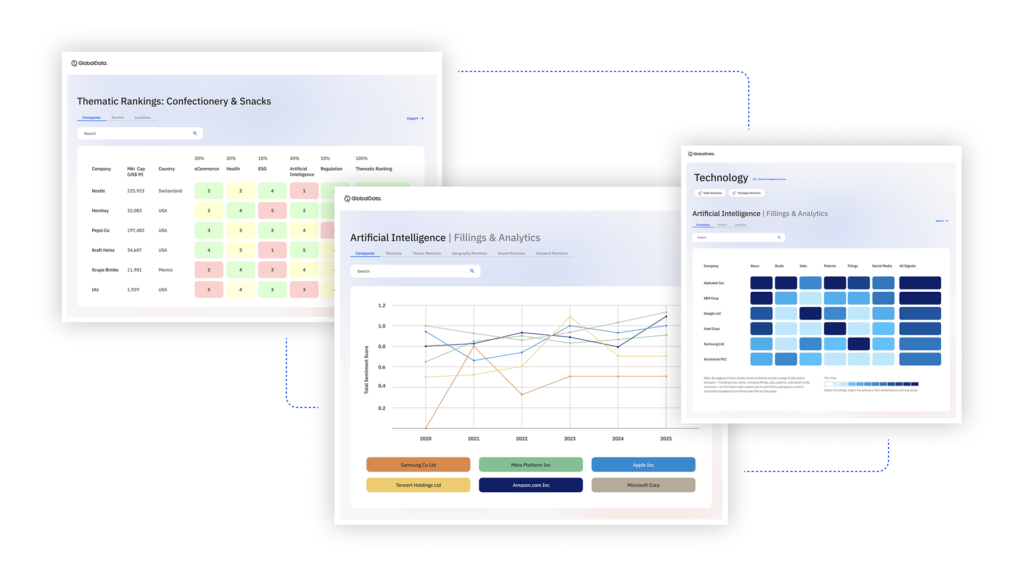
US Tariffs are shifting - will you react or anticipate?
Don’t let policy changes catch you off guard. Stay proactive with real-time data and expert analysis.
By GlobalDataYou’ve got less and less people on board, which means they have an overall knowledge of the ship – they are not specialists anymore. In the old days you had a guy for every discipline on board. But now there is one guy who has to know everything; this means that he knows a little bit about a lot. So the system should have clear diagnostics. The system should indicate what problems you have inside the system, in plain English.
Automation systems should also be able to be repaired by replacement. You take out the old part and put in the new part. Automatically, the system should recognise that and download software from the servers if necessary. The system will indicate which item is broken and locate it physically on board the ship, so the engineer can go there and take out the old one. We’re working with detachable termination so he doesn’t have to take out any wiring, which was often a source of mistakes in the past. He replaces the new part, connects the wiring and the system is back in working order.
Another thing is that, more and more, interfacing with other systems has to be possible. In the old days it was all hard-wired, but now we see more interfaces to other items onboard the ship and also to the shore. You hear more and more questions about shore-based workstations so that the people in the office can see what’s happening onboard the ship.
CL: What kind of financial savings can this level of automation provide to shipping companies?
RvL: I don’t know the numbers exactly, but in one way, it’s mandatory installation so it costs money because you’ve got to have it and it doesn’t allow any extra cargo in the ship. But on the other hand, through the automation, the ship can be sailed in a more efficient way. We deliver quite a number of systems to tankers and to suppliers, and they carry cargo for shore or for platforms.
With our system, you can do it very fast. That means berthing time can be less; in a whole year, they can deliver more cargo. They are also employing fewer people.
That is one of the reasons they have automated the system – it’s a safer ship, but also a more efficient ship.
CL: What was your aim with your Mega-Guard range of automation systems?
RvL: Throughout our deliveries and innovations, we aim to deliver a complete, integrated system. From the alarm and monitoring, through the navigation and DP systems – because DP is a very sophisticated system that not everybody can do – the system has the same hardware and software inside.
So that means trouble-free installation, and trouble-free operation of the ship. They have one I/O board that is suitable for all the systems, so it’s cost-effective. That’s our aim.
CL: Praxis also offers a training system for dynamic positioning – what goes into an effective simulated training programme?
RvL: Not only do you need knowledge of electronics and software, but also an understanding of the dynamic behaviour of a ship in a marine environment. The way we do it is we have a complete simulation of the ship, so we translate the dynamic behaviour of a ship into a module.
Our aim with the training is to simulate the situation onboard a ship during different environmental conditions – storms, rain, large numbers of ships, or certain failures that we introduce during this training. This means that people onboard the ship have been trained for certain situations and will recognise that because the training has been based on real problems.
CL: Are we moving towards a time when all vessel functions are automated, or are there functions that should always be operated manually?
RvL: I was a sailor, and I think that automation will become more and more important due to the reduction in onboard personnel, but also due to the level of knowledge of those people. We see that more and more people from developing countries are being introduced to the workforce because people from the UK and Holland don’t want to sail any more.
It means that the knowledge level is going down, which means that more and more systems have to be automated, and maintenance will also be from the shore. This means that people onshore need to know more about what is happening on the ship.
So it will become increasingly important, but people are always going to be needed onboard, because there are so many situations you cannot force into a module. There are so many parameters that can change; there has to be a human deciding what is going to be done.
CL: Is there a potential future problem with skills in the industry, and an over-reliance on automated systems?
RvL: At the end of the day, we are providing a solution for our customers, who are the ship owners. We see the trend is going this way, if you look at the navigation systems nowadays for example. In the old days they had a sextant and they had to know all about the stars; they had a lot of knowledge of the weather based on the waves and the clouds.
Now you look at an electronic chart and you know where you are and where you’re going, how deep it is and all the rest. That’s the same in the engine room; you don’t have to know exactly where the pumps and the valves are – you push on the screen and the valves will open and the fuel will go to a certain tank and stop once a level has been reached.
That is our task – to make sure that the ships can be operated with the people onboard, and that’s what we’re doing. Our competitors are doing the same.
CL: What automation innovations do you think we could see in the next five years?
RvL: What Praxis is doing is running an ongoing development programme on our systems. We are making our systems better, but also introducing new technology. The shipping business is not exactly in front with the newest developments, so only proven technology is used. But you see more and more integration.
At the moment, we have just launched a new system; we call it the Mega-Guard E-Series, and it means that all the systems are connected to the same network. In the past, we had two networks but now we only have one – that means installation is simpler and the systems can be bigger, the capacity of the systems is getting larger.
We are also paying a lot of attention to the man-machine interface, to make it clearer and better to look at, with nice, clear mimics. On the logging side, we see that there is a big requirement from the ships to do more logging so if people are coming onboard the ship, they can see what has happened in the past on the systems.
Connection to the shore is something we’ll see a lot more of as well, we presume. This kind of internet communication is now more available. In the old days when you wanted to have a short satellite communication, it was very expensive with very narrow bandwidth. Now it’s more available and more affordable than in the past, so one thing will lead to another.