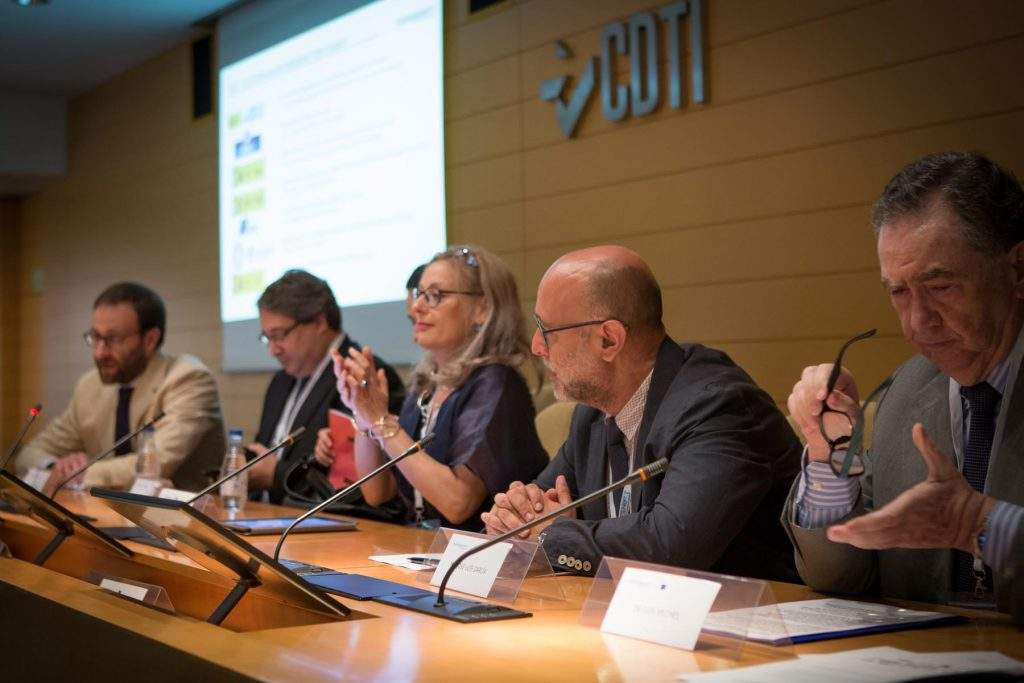
Raul Salinas is the coordinator of the HORIZON 2020 − FIBRESHIP Project.
He works as head of research and international business development at TSI, a vibro-acoustic consultancy company, where he has been involved in several FP7 European projects (BESST, SILENV, AQUO, INCASS). Previously, Salinas was technical manager and partner at design and engineering firm ISONAVAL.
Julian Turner: What are the main objectives of the FIBRESHIP project and how is it funded?
Raul Salinas: FIBRESHIP is driving the development and adoption of composites in the European shipbuilding industry. It will create the knowledge and build the tools for the construction of large composite merchant ships over 50m in length, both seagoing and for inland waterways, thus overcoming the current challenges and technology gaps found in conventional shipbuilding.
FIBRESHIP will develop, evaluate and audit innovative fibre-reinforced polymers (FRP) for maritime applications, prepare new design and production process guidelines, advance efficient production and inspection methods, and adopt leading-edge and empirically validated software analysis tools.
FIBRESHIP is an international consortium of 18 organizations from 11 countries and is part of the
EU 2014-20 Framework Programme, Horizon 2020, which has a total budget of around €80 billion.
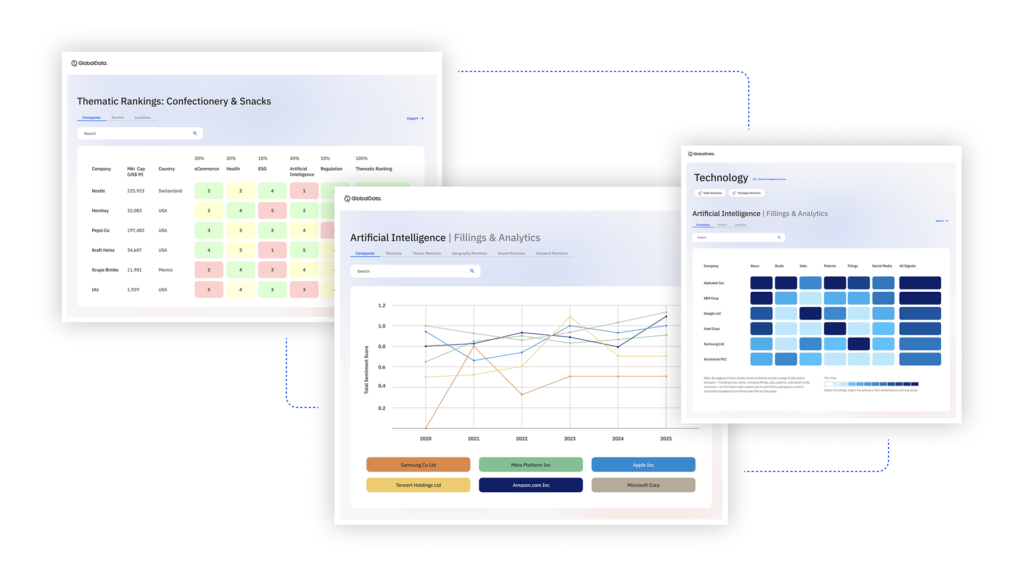
US Tariffs are shifting - will you react or anticipate?
Don’t let policy changes catch you off guard. Stay proactive with real-time data and expert analysis.
By GlobalDataJT: What are the benefits and challenges of FRP materials compared with existing solutions?
RS: FRP solutions have been used for decades in civil and for naval applications. The goal is to realise the full potential benefits of this technology for large-length as well as medium-length vessels.
The new FIBERSHIP FRP materials and construction processes will improve vessels’ efficiency in terms of energy consumption and maintenance costs, offering better solutions for merchant vessels at large.
Potential benefits include a reduction of the structural weight of vessels by 30−40%, significant fuel savings of between 10% and 15%, an increase in cargo capacity of roughly 12% and a 30% reduction in maintenance costs.
In addition, operating cost savings of 7% are predicted for medium-sized container ships and around 3% for larger vessels, plus an increase in recycling ratio from the current 34% to 75%.
Other potential benefits of using the new FRP innovations include greater ship stability, a substantial reduction in greenhouse gas emissions, the ability to continuously monitor the structural health of a vessel, better lifecycle performance due to no corrosion and a better underwater acoustic signature.
The use of FRP materials for ships over 50m long is currently limited to secondary structures and components, largely because of a lack of design and certification guidelines in the event of fire. So, the challenge is to demonstrate that FRP materials do not have a negative effect on safety levels.
JT: How, specifically, does FIBRESHIP plan to achieve these advances in FRP technology?
RS: FIBRESHIP it is an innovation project, meaning that we do not want to reinvent the wheel.
We are focusing on material solutions from other business sectors and how they can be used for marine applications on top of existing solutions that are already in place for small-to-medium vessels. These include retardant resins, intumescent coatings, adhesives and heat dissipaters.
We are going to evaluate an innovative intumescent nanoparticles solution, together with several biomaterials and recycling fibres that may be more cost-effective than current structural materials.
One of the main objectives of the FIBRESHIP project is to establish specific classification society rules for large-length vessels made from FRP materials. In my opinion, this target is realistic because there are several other rules that can be mixed and adapted to achieve this goal. Nevertheless, fatigue analysis and fire-fighting issues remain the most important topics that have to be overcome.
We face a similar scenario when it comes to defining a production strategy for this new business.
An important area of work is the design and extensive use of performance indicators to evaluate different solutions developed for three vessel categories: light merchant ships (container ships), passenger transport and leisure ships (ferries), and special service vessels (oceanographic ships).
The project will develop a comprehensive guide covering design issues and approaches within those three categories that will form the basis for future guides and regulations across all ship types.
The different technologies generated by FIBRESHIP will be tested and validated using advanced simulation techniques and experiments. On top of that, prototypes will be manufactured that can be subjected to real tests in order to demonstrate the functional characteristics of the new materials.
JT: Can FRP only be used to build container ships, ferries and oceanographic ships?
RS: Theoretically, all kind of vessels can be built from FRP materials. Realistically, however, at this point in time the most promising categories of vessels in terms of FRP are the three proposed ones.
These are categorised as “volume transportation vessels” rather than “weight transportation vessels-tankers/bulk carriers”, which have very high fire-fighting and strength requirements.
The FIBRESHIP project will focus on three real engineering cases in these ship categories that have to be solved to the satisfaction of all vessel owners involved in the consortium. At the same time, they will be used as test bench for the development of the required regulations for all kinds of vessels.
JT: How do new validated computational analysis tools inform the FIBRESHIP project?
RS: Analysis software is a powerful engineering tool for designers. However, for FIBRESHIP, they need particular improvements in order to be usable on a daily process.
In particular, software must include fatigue analysis in composite materials for large structures as well as to be able to analyse structure collapse scenarios in case of fire. To achieve this, we started by using COMPASSIS commercial software, which will be updated over the course of the project.
JT: How do you see innovations in shipbuilding materials evolving in the short to medium term?
RS: Europe continues to account for around 40% of civilian and merchant shipbuilding in the world and its advantage is particularly apparent in lighter vessels, with hulls up to 50m in length.
In my opinion, in the medium term, the European shipbuilding industry will lead the construction of large-length vessels in composite materials. There is a new niche market for more efficient and cost-effective vessels of this type, which have a very high added value for owners and ship operators.
In the meantime, we can expect a growing market for larger and larger vessels around Europe based on the defined vessels categories in FIBRESHIP.