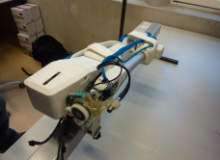
Deep in the bowels of a ship, the ballast water tanks (BWT) are a vitally important but often overlooked part of a vessel. Filled with seawater to help stabilise the vessel when it is empty or partially loaded, the BWT is battered by saltwater and filled up with all manner of marine flora and fauna, which over time cause serious corrosion and fouling. Consequently, the tanks have to be frequently inspected and repaired to ensure they are in working condition.
It’s unfortunate therefore that inspecting and repairing a BWT is a tedious, dirty and occasionally dangerous job. Tanks are often carved out in a part of the ship that has no other function. This means that they tend to be small, oddly shaped and, given their location in the bottom of the vessel, badly ventilated. After a long sea journey, a tank might be full of algae, seaweed and other organic matter which emit a mix of toxic gases.
Consequently, maintenance is not just unpleasant but also expensive. Repairs can only be carried out when the ship is out of service, and with maintenance required every three to five years this costs operators a lot of money – as much as €700,000 per inspection, according to researchers from the University of Twente.
The use of robots is well established for jobs such as inspecting undersea pipelines, so it begs the question of why they have never been used for BWT inspection and maintenance. The main reason, according to scientists from the German Research Centre for Artificial Intelligence (DFKI) and German technology consultant BALance TC, is the “complexity and variability of tank design, as well as the limited flexibility of the available robotic systems.”
BlackBerry has launched a cloud-based Internet of Things (IoT) platform aimed at the lucrative freight shipping market.
A group of Dutch and German technologists known as the RoboShip project may finally have found a way around this.
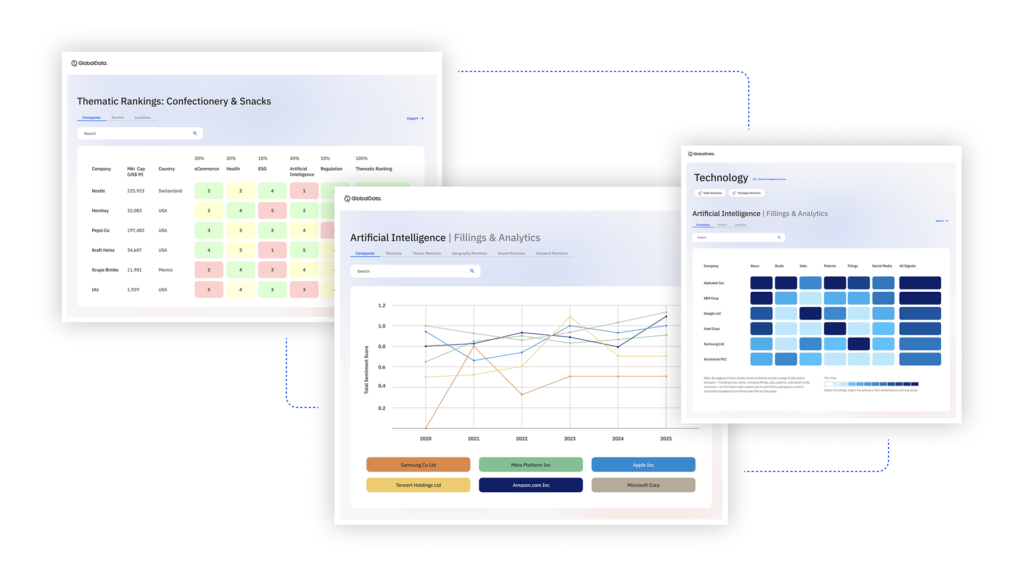
US Tariffs are shifting - will you react or anticipate?
Don’t let policy changes catch you off guard. Stay proactive with real-time data and expert analysis.
By GlobalDataRobots on rails
The RoboShip project is an alliance between the University of Twente, robotic technology developers DFKI Bremen from Germany and Imotec from the Netherlands, formed to explore the potential of intelligent industrial robots in the shipping industry. In late 2014, the project unveiled a robot that can carry out the inspection of a BWT on an ongoing basis, without posing a health risk to workers and, crucially, without having to take the ship out of service.
“I have had the opportunity of seeing the inside of a freighter’s ballast water tank,” says Dian Borgerink, a doctoral student in the robotics and mechatronics department of the University of Twente. “After a voyage, it is slippery with seaweed and is full of noxious gases. Tanks like these are almost inaccessible due to ribs, pipes and cables. Realising that people actually need to go into them to carry out inspection work was what motivated me to develop the robotic arm.”
RoboShip has placed its robot on a set of rails built in to the ballast tank, neutralising the problems caused by variable tank design. Fitted with sensors and a video camera, the robot can move around the walls of the tank, inspect the surface and transmit data back to a central control centre. The robot emits a magnetic field, which allows the controller to identify its exact location and, by proxy, the location of the problem. This can help operators get a better understanding of problems as they unfold and allow them to better schedule planned maintenance.
The robot guides itself by taking several measurements including odometry, inertial measurement unit data and the magnetic field of the tank. “Each tank has a sort of magnetic signature,” Borgerink told futurenautics.com.
Let’s work together
The project was very much a team effort. The rail was developed by Imotec, DFKI built the vehicle itself, while Incas and Xsens – robotics specialists from Germany and the Netherlands, respectively – developed the sensors and tank navigation system. The University of Twente was responsible for the thorough testing of the robot which was carried out at Meyer Werth in Papenburg, a shipyard that has long been at the cutting edge. The shipyard’s management has confirmed that it will integrate the robot into its newly built vessels.
The holy grail, as far as the RoboShip team is concerned, is to modify the robot for repair as well as inspection. It has hinted at the idea of fitting a laser that can carry out minor cleaning and rust repair work. The main barrier is not the technology itself, but how to power it.
“There is always more to investigate and to develop, of course,” Borgerink said. “For now we have proof of principle, which proves that what we designed works, but it still needs some more engineering to make it a full product. The challenge for a laser cleaner is not so much for the robotic arm… The power supply will be more challenging – lasers consume a huge amount of power and increase batteries, weight and so on.”