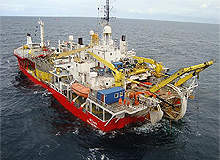
Cable laying company Nexans has been travelling the seas for years, laying cables for communications and energy projects at depths and distances few other companies could achieve.
Recently, the company put its ship, the Skagerrak, into dry dock at Cammel Laird’s shipyard in the UK for a redesign that would see its working space increased. Ship-technology.com spoke with the Nexans team to find out just how this project was carried out, and how modifying its ship has helped business.
Ship-technology.com: The Skagerrak has a long and colourful history. Can you tell us about it?
Nexans: The Skagerrak was built in 1975 by Øgreys Mekaniske Verksted in Kristiansand, Norway to lay cable. Her dimensions were: length 90m, width 33m, turntable capacity 6600t.
In 1981 she got a new bow, new propellers and thrusters. Her width was reduced to 32.1m so that she could to pass through the Panama Canal, and her length extended to 106m.
Owners of the Skagerrak include: Statkraft, Norway (1975-2000); Havila Supply AS, Norway (2000-2003); Bourbon Offshore Norway AS, France (2003-2006), Nexans Norway AS, Norway (2006 onwards).
Project highlights include:
- 1991 Cook Strait, New Zealand (L:120km, D: 260m)
- 1993 Skagerrak III-project, Denmark-Norway (L:130km, D: 550m)
- 1995 Troll A, Norway (L: 67km, D: 350m)
- 1996 Leyte-Cebu, Philippines (L: 130km, D: 310m)
- 1997 Aqaba, Egypt-Jordan (L: 53km, D: 840m)
- 1998 Troika project, Gulf of Mexico (L: 46km, D: 850m)
- 1999 Gemini project, Gulf of Mexico (L: 44km, D:1,034m)
- 2000 Moyle project, Ireland-Scotland (L: 106km, D: 220m)
- 2004 Abu Safah, Saudi Arabia (L: 118km, D: 70m)
- 2005 Guadeloupe (L: 17km, D: 325m)
- 2008 Saudi Arabia-Bahrain (L: 240km, D: 25m)
- 2009 Hainan-Guangdong, China (L: 95km, D: 100m)
How suitable is the Skagerrak today for your key service offering?
The conversion and upgrade has increased its capability to carry out even larger-scale power cable and umbilical installation projects, to meet the changing needs of customers in the subsea interconnector and oil and gas sectors. It has also extended her service life and increased her autonomy while at sea.
The major element in the project has been the insertion of a new 12.5m pre-fabricated hull section that has increased overall length to 112.25m. An additional accommodation module has also been installed – taking the total number of single cabins on board to 60 – together with a new work deck, complete with cable-handling equipment, that has increased the on-deck storage capacity to around 2,000m2 from 900m2. The upgrade has increased the ship’s deadweight from 7,886t to 9,373t.
What makes her so unique?
The C/S Nexans Skagerrak was the first purpose-built ship to be designed specifically for the transport and installation of submarine high-voltage power cables and umbilicals. To date, there are only two vessels of this kind in the world. It features a 7,000t capacity, 29m diameter turntable, a computer-based laying control system and a state-of-the-art dynamic positioning system, and can also deploy Nexans’ specialist Capjet ROV trenching systems for cable burial operations.
The ship can be fitted with additional cable-handling equipment to perform operations such as: cable repairs, including submarine cutting and retrieval of damaged sections; simultaneous laying of two cables with controlled separation; piggyback laying.
Why did you choose the Cammell Laird shipyard to carry out the project?
The Cammell Laird shipyard was selected for the upgrade as Nexans regards it as a reputable company – both technically and financially. It also had the capacity available to suit Nexans’ programme and was competitive on price and conditions. Furthermore, the location of the shipyard in the UK fitted in well with the ship’s route to its next cable-laying project in the North Sea.
You’ve added new accommodation to your ship – why?
In general, the ship is manned by a dedicated crew, who only work on the ship. The accommodation and facilities have been designed to make life more comfortable for them.
Has the investment been worthwhile?
Owning and operating our own dedicated cable ship forms a vital part of Nexans’ strategy to provide a comprehensive service for subsea projects, from design, development and manufacture to installation. This major upgrade and conversion of the C/S Skagerrak underlines our commitment to the subsea sector, and ensures we are well prepared to handle the growing market trend for ever longer cables and larger scale installations.